2 UNITS tow tractor will be sent to
domestic customer. SINOLIFT has unveiled a tugger train system that addresses
the specific requirements of industrial customers, transporting material over
longer distances efficiently, safely and flexibly.
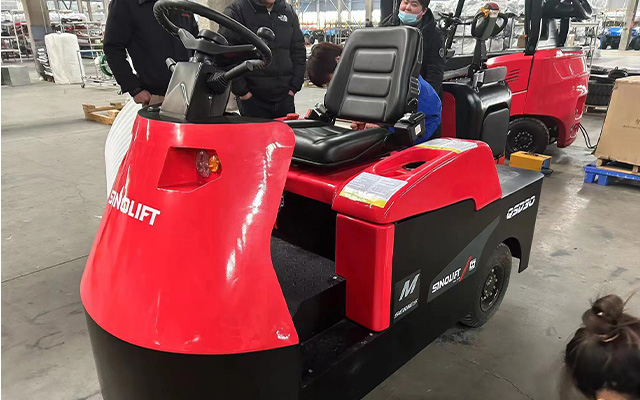
Tugger cart systems work almost identically
to real trains, but on a small, focused scale just right for your operation.
The train itself has a powered tugger operated by a person (like a locomotive)
that tows a connected train of several non-powered carts.
The SINOLIFT tugger train is available as
an all-in-one solution. It consists of the SINOLIFT QSD30 towing tractor with a
towing capacity of 3T trailers. Train systems are one of the first improvement
steps to get away from using forklifts for lineside material movement. They
work as a part of a system to exchange materials and information between the
production area and the warehouse area.
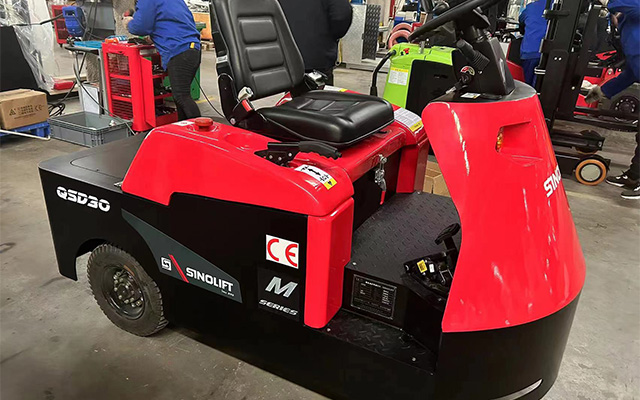
Different cart styles can be used in a
train system – standard carts, mother-daughter cart systems, corral cart
systems, and automatic exchange systems – but they all fulfill the same basic
function.
Critical parts to pay attention to in a
train system are the tow package (tow arm and connecting hitch), cart base
(designed for towing, with aisle width and weight capacity in mind), cart top
hat (when moving totes, boxes, and / or parts), and casters (specified for high
speed towing).
How do they work?
Both tugger cart and forklift deliveries
move materials and information. The differences in how often, how much, and the
movement direction create a clear distinction between the two approaches.
Forklift delivery moves a large quantity of
a single part, very infrequently (because the quantities moved each time are
large), usually in a “push” direction from the warehouse to production.
Tugger cart delivery moves small quantities
of many parts, very often (because the quantities moved each time are small),
usually in a “pull” direction between the warehouse and production.
The tugger follows a standard path with
stops along the way to exchange material, then proceeds to a replenishment area
to then make the same route again. This standardization of material flow
follows the same idea as the standardization of the production process.
Where can tugger cart systems be used?
Tugger cart systems are used successfully
in almost any manufacturing, distribution, or logistics environment. The three
key areas for a train system to function (replenishment, delivery, and
lineside) will look different in each of those operations but the principle is
the same.
There are three critical areas for a cart
system to work well:
Replenishment area
This can be called the warehouse,
supermarket, kitting area, or anywhere else product is prepared to be delivered
to operators. There needs to be a very clear and strong information link
between the lineside area and the replenishment area so that the tugger cart is
loaded with the right materials to supply production.
Delivery aisle
The delivery aisle itself forms the path
that the train will follow on its route, but is often a traffic area shared by
trains and people and needs to be well planned. People have thousands of years
designing standard traffic intersections and still do it poorly, so don’t take
well-planned delivery aisles for granted.Understand the area needed for vehicle
traffic and people. Force delivery traffic into a single lane traveling one way
only. Create visual, bright signage visible for tugger drivers and walking
pedestrians.
Lineside staging
The lineside staging area is a zone between
the operator’s workspace and the delivery aisle. It’s not always a simple
rectangle, but there should be a buffer zone between the operator and the train
route. This is for practical purposes for standard work in process quantities
and material presentation, but also to provide safety for the operator so they
are not disturbed by the traffic. Lineside staging usually takes the form of
flow racks or flow chutes, but cart staging lanes are also used for large parts
or kit carts.
|