Work life as a warehouse associate can be
much easier if a robot tags along. To understand how autonomous robots can transform
what is a physically and mentally demanding job today, it helps to first
understand the day in the life of warehouse work.
A warehouse picker (we’ll call him John)
grabs boxes out of various storage locations, places them onto pallets and then
moves those pallets from one location to the next. On a shipping dock, he’ll
label and wrap his items, write up some paperwork, and start the process again
for the next customer order. John starts his shift at 5 pm and ends it eight
hours later after having walked 5 miles or more inside a 250,000-square foot
warehouse. In that time, he might take just two 15-minute breaks and a dinner
break. He will often be expected to work overtime.
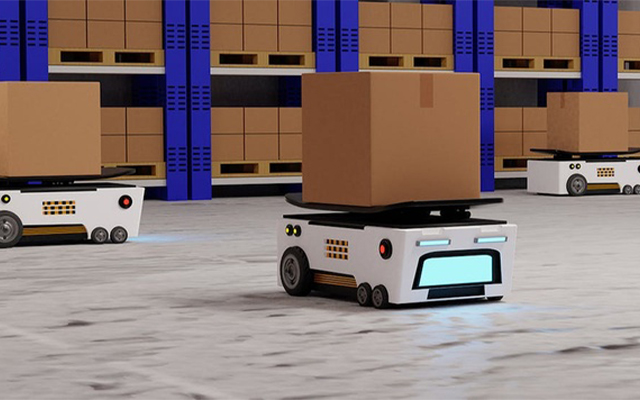
John’s day is physically demanding and can
also involve repetitive tasks. So, any relief John gets to make his experience
more enjoyable will make him a more productive and happier worker.
Introducing an Important Role for Robots
In the days before Amazon acquired Kiva in
2012, if I’d mention robots in a warehouse, I’d be talking about autonomous
guided vehicles (AGVs). These are roving robots that follow wire or tape on the
ground or other visual markers to help guide their set path. AGVs were popular
because they were the first foray into eliminating the need for humans to operate
pallet jacks and the like to move pallets from one location to another. It
eliminated the need for a human driver altogether.
These days, a new generation of warehouse
automation tools, like the Amazon/Kiva robots, bring goods to pickers and a
whole lot more. These are called autonomous mobile robots (AMRs).
AMRs are different from AGVs in
infrastructure and intelligence. AMRs use vision systems like LiDAR (Light
Detection and Ranging) or cameras that operate by learning the environment
dynamically and navigating freely and safely from point A to point B without
human intervention. This technology is similar to self-driving cars.
Without the need to change the warehouse
floor, AMRs can map the territory, travel around freely (as compared to older
technology), and take over a chunk of work that used to be performed by people
(such as driving a pallet or box from the racks to the dock door). Highly
regarded for their safety, ease of use and flexibility, AMRs are not only
contributing to profitability inside the warehouse but also providing a
meaningful solution to the people working alongside of them.
Easy to implement and program, AMRs are
best used as collaborative ‘workers’ next to people. In these ways, warehouse
pickers like John would benefit by:
• Changing the division of labor. A majority of warehouse work is
picking the product and specifically, spending the time handling boxes. AMRs
can make picking more efficient, enabling John to stay within the same aisle or
set of locations in the warehouse, so he can focus on handling product. AMRs
will approach John when there are picks in John’s zone, and when John’s picks
are completed, the AMR will travel to the next zone with that product to see
one of John’s co-workers. In this case, the robot is doing what it does best.
It is traveling around the warehouse handling repetitive tasks with accuracy
and without fatigue. John is doing what he does best. He is solving problems on
how product should be handled and placed onto pallets or outbound containers.
• Reducing worker travel. Depending on the type of orders and size of
the warehouse, travel can occupy anywhere from 30% to 70% of a person’s day.
AMRs can take over much of this in-warehouse travel and automate product
movement. This reduces the burden on warehouse workers having to drive from one
side of the warehouse (where product is located) to the other (where orders are
packed and shipped), and also reduces the physical strain of walking.
• Taking control. Without the need to understand programming
language, John can task his AMR to help him with his picking tasks, through
various means. One way is through John’s interaction on a screen attached to
the robot, tapping to begin next action, which prompts the AMR to act. In more
sophisticated operations, John follows instructions on his handheld device or
uses voice interaction to capture what work he completed and, through warehouse
optimization software, the AMRs move alongside him automatically without John’s
direction. John has the peace of mind knowing his companion won’t tire or call
off work.
Companies Are Spotting and Adopting this
Smart Strategy
Companies, worldwide, are identifying the
value of this collaboration and investing in it. For instance, fleet management
company Ryder System Inc. recently announced that it implemented multiple types
of AMRs in three different DCs to provide its workers assistance in reducing the
burden of labor-intensive tasks and travel.
Two workers—one human and one robot—sharing
tasks effortlessly and in harmony throughout the warehouse floor is not a
sci-fi scenario. It’s happening today. The key to making this elegant
collaboration work well resides in the systems and software integrating the
human/robot experience.
Integration means understanding how humans
and robots should interact to accomplish the work normally done 100% by humans
and how to make that experience as seamless as possible. How does the robot
know where to go next to connect up with a person? How is the person
communicating with a robot so that tasks aren’t duplicative or—even
worse—missed?
A New Breed of Software
A set of software solutions, referred to as
a warehouse optimization suite, are applied to bridge the gap and orchestrate
warehouse work seamlessly. These software solutions understand all the work in
the warehouse and manage completion of those tasks, electronically capturing
results in real-time as tasks are completed on the floor. The process is more
sophisticated than traditional warehouse control systems as it provides the
intelligence in how these tasks are scheduled dynamically as opposed to a
static work plan which is setup in advance and executed in a simple order. This
ensures the right sequence of work is completed at the right time to ensure all
customer demands are met, especially as warehouse conditions change such as
trucks being rescheduled, which may require reprioritizing work.
These systems include both AMRs and people
in understanding the real-time location of the work. As an emergency order
comes into the warehouse, it is immediately assigned to the next AMR. Given the
system’s knowledge of all product needed for that order, the warehouse optimization
software directs the AMR to the first area to be picked and also notifies John
to go to this same location to meet up with it automatically. As John completes
the pick and captures the result electronically, the AMR goes to the next
warehouse location where John is also directed to go by this software. This
continues until John completes the last pick in his area and the AMR goes to
packing to be completed and shipped out ASAP. This is all directed through the
sophisticated orchestration software.
In scenarios like this, the day in the life
of a warehouse worker is greatly improved. You might wonder when this dynamic
duo make sense?
1. An abundance of product (SKUs). To
achieve the best ROI, organizations should be already managing a large number
of SKUs or associated volume of product which, in turn, requires a large
warehouse for storage. Large SKU volume would most likely require a sizable
amount of in-warehouse travel which could then be reduced with AMRs.
2. Workers must support the model. The
workforce should welcome this AMR+people scenario. I’ve heard management wonder
if the use of robots will shift skills away from warehouse workers, minimizing
their future employment. I believe just the opposite. Assigning robots the
repetitive tasks will free up people to take on higher-level problem-solving
tasks, sharpening their skills and improving their own personal productivity.
This can provide them more economic opportunities in the future. According to a
recent Harvard Business Review study focused on warehouse worker perceptions,
respondents were enthusiastic about the use of technology if it helped them be
faster, safer and more efficient.
3. It’s not displacement. Some in the
industry express fear that robots will completely take over the role of the
associate. I believe this displacement theory is a myth. There’s plenty of work
to go around. Consider that the U.S. is experiencing a nationwide labor
shortage—and this is especially prominent among delivery drivers and warehouse
workers. In the last six years, the number of job openings in the warehouse and
transportation industry has doubled—shifting from 200,000 openings in 2015 to a
record 490,000 in 2021, according to the U.S. Department of Labor. The actual
number of open jobs is even higher than that when you add in seasonal workers
and consider that retailers, manufacturers and distributors all have warehouses
and may not have been included in those original figures. The industry is
growing at a rate that minimizes the validity of the displacement theory.
Making Life Better for the Warehouse
Associate
People will always be needed for warehouse
work that requires specificity and judgment. For example, people (not robots)
are best suited to handle products which have variations in sizes, packaging
and texture. Even the rigidity of packaging may require a customized approach.
A pallet may be sitting off-center a bit or boxes are not stacked in the right
order, or some boxes are dented. These fixes require people to reason through
and address.
Additionally, as consumers turn to ordering
more online, e-commerce has created complexities in picking for which people
are ideal. For example, workers might not pick boxes but rather individual
items of unique geometry such as cylinders for two-liter soft drinks or long
thin bars. This is much easier done today by people rather than robots.
The New Workforce = Workers + Robots
AMRs and people effortlessly working
side-by-side on the warehouse floor is a scenario of the future of warehouse
work. Investing in this modern collaboration will not only help you obtain
better productivity, accuracy, safety and efficiency, but will also provide more
meaningful work to people like John.
Re-distribute tasks so that people and
robots each do what they do best. This will contribute to more job satisfaction
of warehouse workers. During this time of labor shortages, worker satisfaction
is key to retention—and recruitment.
Adding AMRs to your worker mix may help you
address the overall labor shortfall, and aid in business continuity at a time
when millions of U.S. workers have left their jobs.
Robotics are just a natural extension of
all the automation transforming warehouses and DCs over the last two decades as
a way to improve overall cycle times and throughput as all companies strive to
compete with Amazon’s same-day shipping and next day delivery promises. It
should be welcomed for the smart efficiency it brings to everyone involved.
The technology to support robots/people is
ready and it works. In the case of Ryder Systems, they produced a 25% increase
in productivity simply by reducing travel time in the warehouse.
Robot/people collaborations are fast
becoming a focus and could be your competitive advantage in the coming year.
Consider it to fine-tune your operations and provide meaningful work to your
employees.
Ron May is founding member and senior
solution consultant at Lucas Systems, a provider of smart software for
warehouse managers and on-floor workers.
|